Sand casting
In addition to red bronze and bronzes we also cast multi-alloy bronzes, lead bronze as well as brass and special brass with unit weights up to 1000kg according to DIN EN 1982. In addition, we cast all aluminium alloys according to DIN EN 1706 (unit weights up to 150kg) as well as steel and stainless steel alloys (unit weights up to 4000kg).
Machine mould casting:
For machine mould casting for non-ferrous metals and aluminium we have a moulding machine (Dynamatic Aspa 300) with box dimensions 610x460x225/225 available.
Hand-moulding:
For hand moulding the box dimensions range from 600x600x300 to 2500x2000x600.
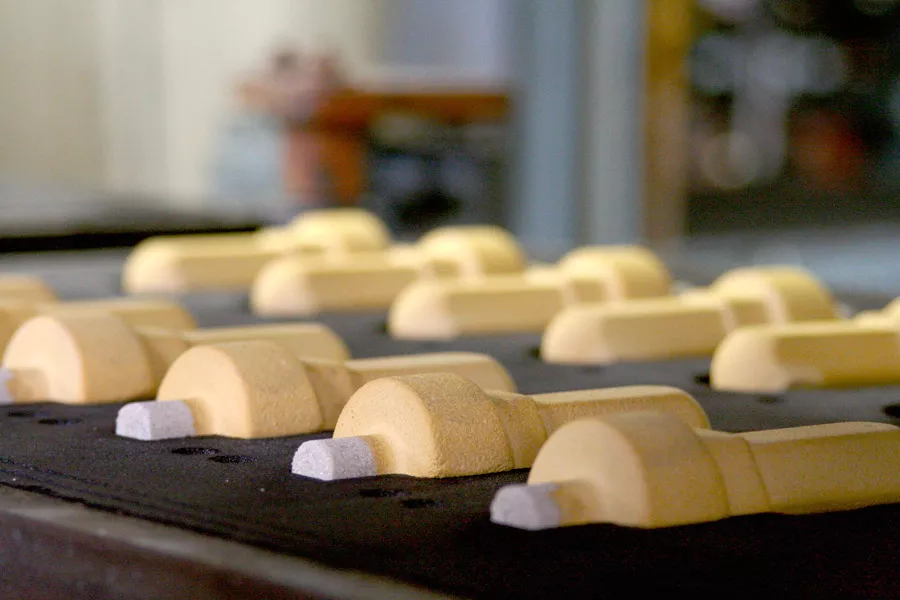
Cores for sand casting
Sand casting process
The process of sand casting belongs to the group of shell mould casting processes. Shell moulds are usually made of sand with suitable binding agents.
Moulding requires a model or pattern of the casting that must be made to compensate for the shrinkage of the casting material during cooling in the solid state with an allowance (shrinkage).
The mould is therefore made from two separate moulds, the cope and drag halves, so that the model can be retrieved before casting. The model must have “draught angles” so that the sand mould is not damaged during removal of the model.
Subsequently, the cope and drag halves are accurately fitted together and the liquid metal is poured into the mould.
To compensate for the shrinkage in the liquid state and during solidification, one or more feeders are installed. Cavities and undercuts on the casting are shown with sand cores. In general, castings are moulded on both sides.